Le groupe SagemCom est l’un des six constructeurs du compteur Linky choisis par Enedis. Un partenariat industriel qui bénéficie à la seule usine française du groupe, située près de Dinan, en Bretagne.
| Cet article fait partie du dossier « Linky, le compteur de toutes les attentions »
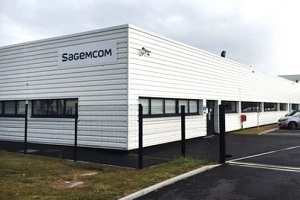
L’usine bretonne de Sagemcom est passée d’une production de consommables d’impression (fax et imprimantes) à un site industriel produisant plusieurs millions de compteurs communicants multi-energy (Sagemcom MEI) par an et employant une centaine de personnes.
500 000 compteurs Linky sont livrés chaque mois à Enedis. Pour assurer une telle production, plusieurs industriels ont été mis à contribution par la filiale d’EdF, dont le Français Sagemcom. Ce dernier dispose d’une seule usine en France, entièrement dédiée aux compteurs communicants Linky (électricité) et Gazpar (gaz).
Sagemcom Multi-Energy Industry (MEI) est située sur la zone industrielle de Taden, à Dinan (Côtes-d’Armor). D’ailleurs, à peine quitté le centre-ville de cette bourgade bretonne, on aperçoit rapidement les bâtiments blanc et noir de Sagemcom MEI. L’industriel a investi 12 millions d’euros depuis 2009 dans cette usine qu’il a entièrement reconvertie dans l’assemblage des compteurs communicants, jusqu’à l’exécution des tests de bon fonctionnement de chacun. Seules, les cartes électroniques sont livrées depuis une autre usine du groupe, située en Tunisie, de même que les capots plastiques verts et gris du compteur, en provenance de l’usine Plastivaloire de Mamers (Sarthe).
[bctt tweet= »#Linky – 500 000 compteurs Linky sont livrés chaque mois à Enedis. » username= »Alliancy_lemag »]Une usine automatisée conçue autour du produit
« Dès le départ, pour décrocher cet appel d’offres, nous avons tablé sur le Made in France et la certification ISO 27001. Mais ceci n’était envisageable qu’à condition de passer par la robotisation du process industriel pour des questions de qualité, de volumes à produire et de coûts. Une nouvelle architecture que nous avons entièrement conçue autour du produit et développée en interne », explique Thomas Ghier, industrial & logistic Core Business Director du groupe. Je ne m’étonne donc pas de voir gesticuler les bras articulés des robots tout au long de la visite.
Ensuite, une fois sortie de ce module, la production journalière de compteurs Linky peut être emballée ; puis expédiée par camion vers l’entrepôt lyonnais de Sagemcom, avant d’être redistribuée à la demande vers l’une des onze plates-formes logistiques Serval* d’Enedis. La traçabilité complète des composants, des outillages, des produits et des flux est assuré via la solution SAP Manufacturing Execution (SAP ME), qui communique directement avec les systèmes d’information d’Enedis et Serval.
L’usine, qui tourne en trois-huit sur 5 jours avec 85 salariés (dont 32 reconvertis), atteindra son premier pic de production mi-2018 avec plus d’une centaine de personnes. Elle assemblera alors entre 7 500 et 8 000 compteurs communicants par jour (+ de 3 millions d’unités produites en 2017). A date, plus de 2,5 millions de compteurs Linky ont été livrés à Enedis, soit plus de deux fois le contrat de départ, décroché fin 2014.
Un énorme marché à l’international
Mais, le marché des compteurs communicants ne se limite pas à la France, ni à l’énergie (pourquoi pas à la chaleur, à l’eau…). La directive européenne Efficacité énergétique, qui a impulsé ce déploiement pour l’ensemble des Etats-membres, prévoit que 80 % des foyers européens soient équipés de compteurs communicants à l’horizon 2020. Déjà, l’Italie (32 millions de compteurs), la Suède (5,2 millions) ou la Finlande (3,1 millions) ont terminé leur déploiement… et un rapport du cabinet Navigant Research a même estimé que leur nombre dans le monde pourrait dépasser le milliard d’unités à l’horizon 2022 (700 millions aujourd’hui).
Aussi, au-delà de Linky et Gazpar qui lui offrent une vitrine unique par l’ampleur du déploiement et le niveau technologique requis, Sagemcom vise à court terme l’export. « Les grands projets de ce type vont arriver en Europe, précise Thomas Ghier. En ce sens, Linky a un vrai avantage. C’est un produit avec peu de variantes, qui offre une durée de vie commerciale de plus de cinq ans. » De quoi amortir l’investissement et en faire bénéficier toute l’économie locale. D’ores et déjà, 250 emplois indirects ont été créés dans le bassin d’emploi grâce à la nouvelle usine de Dinan (transport, plasturgie, robotique…). « Nous sommes le centre d’excellence dans ce domaine pour notre groupe désormais », conclut optimiste le cadre dirigeant.
* La Supply Chain de Linky dispose de 11 plates-formes logistiques Serval en France, filiale d’Enedis (Saint-Quentin, Nancy, Lyon, Aix-en-Provence, Toulouse, Bordeaux, Riom, Orléans, Ploërmel, Caen et Gennevilliers). Soit, au total, 88 000 mètres carrés d’entrepôts et 165 000 mètres carrés de parcs extérieurs.
Le process de fabrication du compteur Linky
Tunis (Tunisie)
- Fabrication et tests électriques et fonctionnels des cartes
- Montage dans le berceau et conditionnements
Dinan (Côtes-d’Armor)
1/ Test de la carte électronique
- Réception de l’ensemble des composants (cartes, capots plastiques, etc.)
- Le 1er robot déconditionne les cartes, puis les insère dans une machine de réglages et de tests.
- De préhenseurs spécifiques ont été développés pour permettre la manipulation des cartes
2/ Assemblage du produit
Le deuxième robot permet l’assemblage des éléments mécaniques et électroniques.
3/ Test produit complet
Les produits intégrés sont ensuite convoyés pour réalisation de tests.
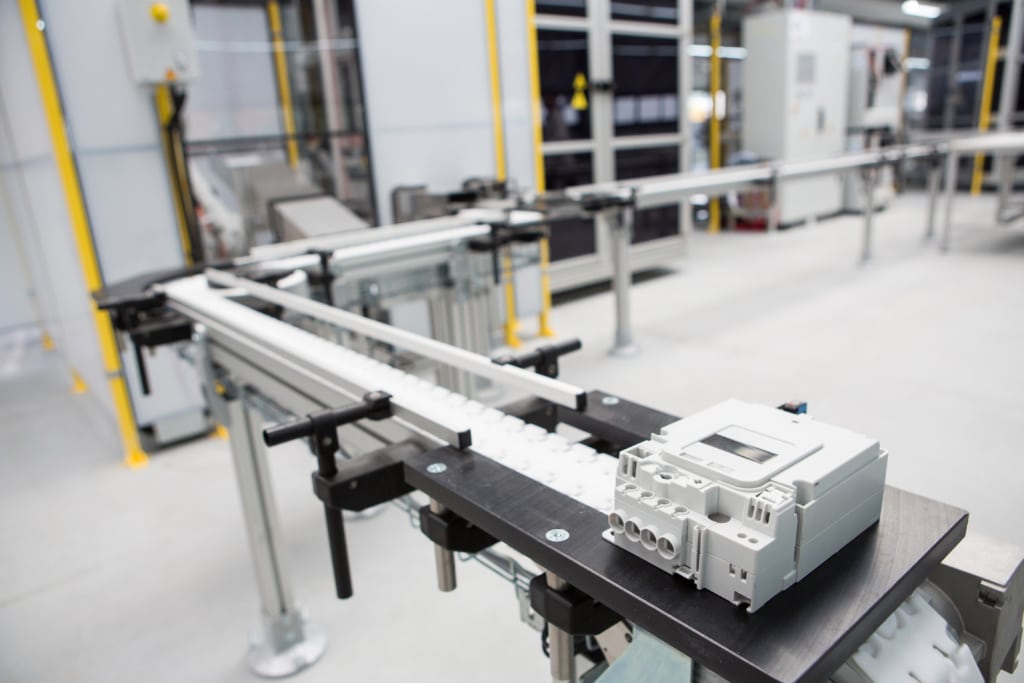
Sortie convoyeur – L’usine bretonne de Sagemcom @Sagemcom
4/ Sortie convoyeur pour test
Les produits intégrés arrivent dans le 2ème module.
5/ Produit fini
- En fin de ligne, le produit est intégré, réglé, marqué et scellé.
- Resteront ensuite les tests sur le produit complet à réaliser, le marquage laser et la sérialisation ; la personnalisation et l’intégration des clés ErDF, l’emballage et la mise en palette.
Quarante ans dans les télécoms
1924 : Naissance de Sagem dans les outillages pour machines-outils.
2008 : Sortie de Sagem Communications par LMBO avec le fonds d’investissement américain Gores.
2009 : Sagem Communications devient Sagemcom.
2011 : Second LMBO avec le fonds d’investissement américain Carlyle
2016 : Le britannique Charterhouse Capital Partners devient actionnaire majoritaire à 70 % de Sagemcom. Les salariés conservent 30 % du capital.
Un acteur européen
Effectif 4 000 salariés, dont 1 000 en France
Chiffre d’affaires 1,7 milliard d’euros en 2017, dans 40 pays
R&D 450 ingénieurs en Ile-de-France (wifi, sécurité, data…)
3 activités : Broadband (décodeurs, passerelles résidentielles) ; Energie et télécoms (compteurs communicants, gestion sites en Afrique…) et IOT (capteurs Lora).
Sites de production : 1 en France (compteurs communicants) ; 2 en Italie (compteurs gaz) ; 1 en Allemagne (développement logiciels, compteurs communicants) ; 1 en Tunisie (toutes activités) et 1 au Brésil (Broadband pour toute l’Amérique du Sud).
30 millions de terminaux fabriqués par an
Source : Sagemcom