Le groupe Schneider Electric dispose désormais de sa vitrine « Industrie du futur », au Vaudreuil dans l’Eure, un site pilote en matière de transformation numérique inauguré ce mardi par Jean-Pascal Tricoire, PDG du groupe.
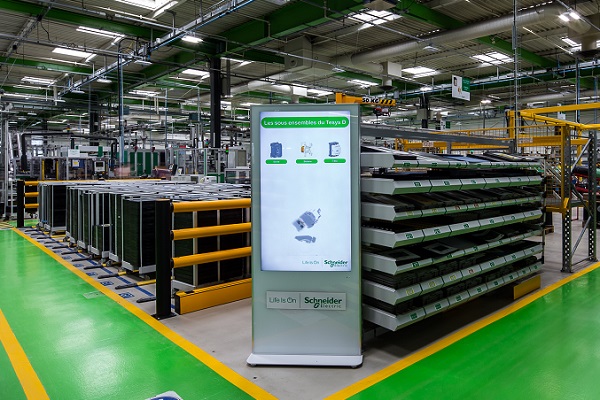
Site Industriel Le Vaudreuil (Eure) – vue intérieure ©Schneider Electric
Lors du salon Global Industrie, l’Alliance Industrie du futur (AIF) remettait au groupe Schneider Electric pour son usine du Vaudreuil (Eure), le label « Vitrine Industrie du Futur ».
Un label qui récompense les entreprises « ayant développé concrètement un projet novateur et mis en œuvre une fourniture de solutions technologiques ou méthodologiques d’origine majoritairement française ».
Quelques jours plus tard, ce 3 avril, c’était le grand jour de l’inauguration du site, fraîchement repeint pour l’occasion. En présence de tous les acteurs publics locaux et de Sébastien Lecornu, Secrétaire d’État auprès du ministre de la Transition écologique et solidaire, Jean-Pascal Tricoire, PDG du groupe, admettait toutefois : « Ne nous trompons pas, notre concurrence est mondiale et vient de tous les continents. Et notre marché est mondial lui aussi : 98 % de nos ventes en protection et contrôle moteur s’effectuent hors de France. En témoigne d’ailleurs cette usine du Vaudreuil. En 2017, plus de 10 millions de contacteurs et 100 000 drive et starters produits ici ont été vendus. 80 % de la production est exportée. Il n’y a donc pas d’autre choix que d’être les plus innovants et les plus compétitifs. Pas simplement au niveau français, pas simplement au niveau européen, mais tout simplement et sans hésitation au niveau mondial. »
Journée historique pour le Vaudreuil, @jptricoire accompagne cette transformation digitale avec toutes les équipes de Schneider Electric. #IndustrieduFutur #SchneiderElectric pic.twitter.com/O2D87XH2cA
— Schneider Electric France (@SchneiderElecFR) April 3, 2018
Créé en 1975, le site normand compte 360 collaborateurs. Spécialisé pour le pilotage et la protection des moteurs industriels, il produit des contacteurs et des variateurs de vitesse. L’usine a obtenu le label « Industrie du futur » pour sa démarche d’expérimentation rapide, pour la mise en place de solutions de monitoring et de maintenance prédictive via la réalité augmentée. Un projet qui s’inscrit dans un contexte de production haute cadence pour l’amélioration de la compétitivité de plus de 20 % d’ici à 2020, mais également pour l’amélioration de la relation client. Plusieurs grands clients du groupe étaient d’ailleurs présents à l’inauguration… et l’agenda des visites est plein jusqu’en septembre prochain.
Serge Catherineau, directeur marketing Industrie Automobile, Aéronautique et Système Intégrateurs pour Schneider Electric, rappelait d’entrée les défis que va permettre de relever cette transformation numérique : « Ils sont de quatre ordres et concernent à la fois la disponibilité opérationnelle de l’outil de production ; la performance industrielle ; la flexibilité des hommes et l’efficacité énergétique. »
Des « POC » aux points critiques
Pour parvenir à cette évolution, une équipe projet dédiée a été créée sur le site du Vaudreuil, incluant des compétences techniques et organisationnelles pour identifier et mener les Proof of Concept (PoC) sans perturber la production, tout en accompagnant le changement de compétences.
Dès l’entrée de l’usine, des changements sont visibles. Au-delà du mini-datacenter qui stocke localement l’ensemble des données critiques du site, une borne de décontamination pour clés USB a été installée et doit impérativement être utilisée par tous les collaborateurs et externes qui souhaitent travailler temporairement sur le site. Un système qui a permis de réduire de 80 % le nombre d’incidents.
Un peu plus loin, on passe à la traçabilité. Des capteurs ont été installés sur les bobineuses qui permettent de suivre en temps réel la température des axes rotatifs pour anticiper ainsi les changements de composants défectueux avant même que ne survienne les incidents… « L’installation, mise au point avec l’aide d’une start-up, a coûté 6 000 euros, mais elle permet un gain de 20 000 euros sur l’année », précise l’opérateur. « Grâce à cela, ajoute Serge Catherineau, on arrête régulièrement les machines deux heures maximum pour maintenance contre 7 heures précédemment. »
En poursuivant la visite, on découvre une application de réalité augmentée, également mise au point pour les opérateurs de maintenance. A l’aide d’une tablette, ceux-ci peuvent accéder aux multiples informations techniques relatives à une pièce avant même d’avoir à ouvrir le capot de la machine… Ce qui permet de gagner 80 % du temps sur l’analyse et l’arrêt du matériel et un début très prometteur pour aller vers l’usine « zéro papier ». Cette accélération du diagnostic, associée à la digitalisation des retours d’informations au technicien sur des pannes ou des anomalies, permet ainsi d’augmenter significativement le temps de production des moyens (de 5 à 15 % selon les lots).
L’usine du Vaudreuil est le premier site du groupe Schneider Electric en Europe à bénéficier du programme de transformation interne « EcoStruxure for industry », également mis en œuvre dans une autre usine en Chine.
On verra également dans l’usine, la mise en œuvre d’un seul cobot Rethink Robotics pour le contrôle qualité des produits, et croiserons quelques AGV Fybots, appelés « tortues » pour l’approvisionnement des produits et « tracteurs » pour le transport des produits finis.
Enfin, un système intégré de gestion du bâtiment permet de modéliser et faire des économies d’énergie. Objectif : réduire de 4 % la facture gaz et électricité par an jusqu’en 2020, qui s’élève pour 2017 à 700 000 euros. Suivi des pompes à chaleur, capteurs de CO² dans les ateliers… Le site a déjà largement économisé sur le volume d’air à chauffer ou à réfrigérer.
« En organisant des filières de recyclage pour tous nos déchets suivant leur provenance, en produisant nous-même de l’énergie renouvelable – ici, avec 28 mètres carrés de panneaux, nous produisons déjà l’éclairage des bureaux – ou en l’achetant, nous visons la neutralité carbone dans notre écosystème en 2030 », a précisé Jean-Pascal Tricoire.
Cet ensemble de « briques technologiques », issues de l’offre du groupe « EcoStruxure for Industry » et testées sur ce site « vitrine » en Normandie, devrait être déployé à échelle industrielle sur une centaine d’usines du groupe de Schneider Electric d’ici à 2020. EcoStruxure (architecture et plateforme système ouverte, interopérable et compatible IoT) est déjà présent dans plus de 480 000 installations aujourd’hui, avec le soutien de 20 000 intégrateurs de systèmes et connecte plus de 1,5 million d’actifs.
A lire aussi sur Alliancy