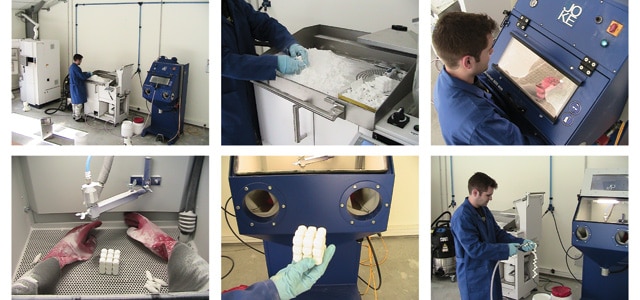
Repositionné sur le marché des entreprises, Sculpteo ambitionne de devenir un acteur majeur de l’impression 3D en Europe et aux Etats-Unis. La start-up francilienne vient de boucler son deuxième tour de table (une augmentation de capital de 5 millions d’euros) et publie une étude internationale sur l’usage actuel de cette technologie (www.sculpteo.com/fr/get/report/state_of_3D_printing_2015). Ici, l’atelier de production situé à Arreau, dans les Pyrénées, qui abrite la Formiga P100 de Eos, permettant la production d’objets en plastique blanc. © Sculpteo
Les machines professionnelles de fabrication additive sont désormais considérées comme une technologie clé pour l’industrie. Un regain d’intérêt suscité par la redécouverte de leurs atouts et le passage du prototypage à la production de pièces fonctionnelles.
Il en est des technologies comme des acteurs. Certains n’accèdent aux premiers rôles qu’à l’âge mûr. La fabrication additive, plus connue sous le nom d’impression 3D, fait partie de ce lot. Depuis son invention, au milieu des années 1980, elle était cantonnée aux seconds rôles. On l’utilisait pour réaliser très vite des pièces prototypes, généralement en plastique. Il faut dire qu’elle s’y prête parfaitement. Pas besoin de concevoir des outillages complexes pour la produire. Il suffit de la créer en 3D sur écran et de cliquer, comme pour une impression. En un rien de temps la pièce est prête. Magique… Joseph Puzo, patron du fabricant de connecteurs Axon’Câble raconte : « Avec cet outil, nous pouvons très vite présenter la maquette de son produit au client et, s’il souhaite des modifications, nous avons la possibilité de les effectuer sur le champ et de lui montrer le résultat avant qu’il ne reparte. » Voici maintenant que l’impression 3D a acquis le statut de star. Elle est devenue l’un des outils les plus prisés de la révolution industrielle en cours. Cela parce que, d’une part, l’arrivée de machines bas de gamme (de l’ordre d’un millier d’euros) lui a fait une formidable publicité. Parce que, aussi, les produits professionnels qui, eux, coûtent des centaines de milliers d’euros, ont évolué et savent produire des pièces dans une panoplie de plus en plus vaste de matériaux, des polymères aux métaux comme l’acier, l’aluminium, le titane, en passant par les céramiques…
La vraie raison du succès est ailleurs, toutefois. Cette évolution s’est accompagnée d’une formidable (re)découverte des atouts de la fabrication additive : elle permet de réaliser des pièces de forme aussi complexe qu’on le souhaite. Des pièces parfaitement impossibles à concevoir par tout autre procédé. Par exemple, si on le désire il est possible de fabriquer d’une seule pièce une chaîne de vélo parfaitement fonctionnelle sur une imprimante 3D ! Cela change complètement la donne.
Jusque-là en effet, on n’utilisait ce mode de production uniquement comme alternative aux outils classiques. Par exemple, une pièce avait été conçue pour être usinée, mais pour différentes raisons (prototypage par exemple), on était amené à la produire sur une imprimante 3D. Désormais, la perspective s’inverse. La pièce sera conçue pour profiter des caractéristiques inouïes de la fabrication additive et cela ouvre de nouveaux horizons. On peut ainsi profiter de la technologie pour réaliser une pièce unique de forme complexe qui remplacera un assemblage de plusieurs sous-ensembles. C’est ce que fait par exemple Dassault Aviation pour des conduites d’aération en polymère à l’intérieur de l’habitacle d’un avion. Mieux encore, il est possible de concevoir des pièces de façon totalement originale mêlant des formes complexes à des architectures que seule la fabrication 3D autorise. Cela peut conduire à un allégement considérable – un poids divisé par un facteur deux ou trois – ou à des produits totalement innovants comme des implants maxillo-faciaux sur-mesure par exemple.
Atteindre la production en grande série
Reste l’inconvénient majeur : elle est encore inadaptée à la production en grande série. Il faut quelques heures pour produire une pièce là où, une fois que tous les outillages ont été mis au point, il suffit de quelques secondes (dans le cas du moulage par injection de plastique par exemple) ou de quelques minutes (dans le cas de l’usinage de métal). Même si les machines poursuivent leur évolution et permettent déjà de réaliser des petites séries, cette caractéristique limite encore fortement la pénétration de l’impression 3D dans tous les secteurs de l’industrie. Va pour l’aéronautique où elle se fait peu à peu une belle place au soleil. Les séries sont limitées et c’est là qu’il est possible de tirer le meilleur profit de ses atouts : pièces hypercomplexes et considérablement allégées. L’industrie automobile, en revanche, est encore loin d’en faire ses choux gras…
L’impression 3D trouve ainsi peu à peu des niches où elle peut exprimer ses atouts : fabrication unitaire ou en petite série de pièces de formes et complexes et/ou sur mesure. Ce sont par exemple, outre l’aéronautique, le domaine dentaire (guides de perçage pour les implants, couronnes…), l’orthopédie (pièces ancillaires pour positionner des implants, orthèses…) et le médical au sens large. Des moulistes, comme la société Compose (Ain) par exemple, l’utilisent également pour produire des moules d’injection hors normes où les conduits de refroidissement ont des formes si biscornues que l’usinage classique ne permet pas de les réaliser. Il est un autre type d’application qui se développe : la fabrication de pièces détachées sur site. Ainsi, dans l’aéronautique, la maintenance des avions exige de disposer sur site de pièces extrêmement coûteuses, mais très rarement utilisées. Pourquoi ne pas s’affranchir du coûteux stockage et les fabriquer à l’aide d’une machine 3D que lorsque le besoin s’en fait sentir ? Idem pour les navires. Ils embarquent d’encombrants stocks de pièces détachées alors qu’une machine 3D permet de faire face rapidement au remplacement d’une pièce (lire page 68). Il ne fait aucun doute que le champ d’applications de la fabrication additive va s’élargir à mesure que les performances des machines s’amélioreront.
Cela dit, le frein à sa diffusion ne tient pas seulement aux limitations imposées par la technologie. Il est également culturel. Pour exploiter pleinement ses multiples atouts, il faut en effet que les bureaux d’études révisent complètement leurs pratiques et apprennent à concevoir leurs produits d’une façon radicalement différente. Ce n’est pas le moindre des défis.
>> Retrouvez l’intégralité de notre dossier dédié à l’usine du futur