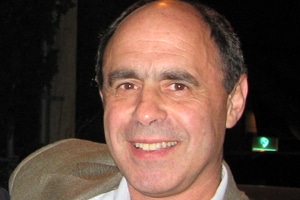
Ron Beck, Engineering Director, AspenTech
La maîtrise de l’énergie est essentielle à la viabilité et la rentabilité de toute opération. L’énergie est après les matières premières le deuxième principal poste de dépenses pour la plupart des procédés chimiques et de raffinage. Les raffineries et usines pétrochimiques qui investissent dans l’efficacité énergétique gagnent en compétitivité grâce à l’amélioration de leur marge opérationnelle, de leur flexibilité de production et de leur bilan carbone. L’optimisation de la consommation d’énergie doit être perçue comme une opportunité pour l’entreprise et intégrée à tous les aspects de son activité. Des facteurs internes et externes font de cette optimisation un défi permanent dans toute opération. Les sources, l’offre et le coût de l’énergie évoluent. Les fluctuations des matières premières obligent les entreprises à ajuster leur stratégie d’exploitation. Les contrats de vente leur imposent des contraintes. La réglementation et la fiscalité environnementales peuvent les forcer à modifier leurs processus de production tandis que les équipements vieillissent au fil du temps et que leur état affecte l’efficacité opérationnelle (par ex. l’encrassement des échangeurs de chaleur vieillissants).
Par conséquent, que peuvent faire les entreprises du raffinage et de la pétrochimie pour ne pas perdre de vue l’efficacité énergétique dans le contexte de complexité et d’incertitude actuel ?
Lorsqu’on aborde la question de l’efficacité énergétique, il faut considérer séparément les aspects liés à l’offre et ceux liés à la demande. Côté demande, différentes stratégies sont possibles pour réduire les besoins en énergie. Il s’agit essentiellement de mieux utiliser toutes les sources de chauffage et de refroidissement d’une usine. On parle alors d’intégration thermique ; notion abordée lors de la conception mais aussi en phase d’exploitation de n’importe quelle installation. La demande peut être réduite en améliorant le fonctionnement et la maintenance des équipements. Les échangeurs de chaleur rencontrent diverses difficultés opérationnelles allant de l’encrassement des surfaces de transfert thermique, aux vibrations et aux problèmes hydrauliques. Les stratégies de procédés peuvent avoir une incidence significative sur la consommation énergétique, par exemple le réglage de la température de fonctionnement ou l’ajustement du plateau de colonne et du flux. En réduisant la variabilité des processus (via l’optimisation et le contrôle en temps réel), on peut aussi considérablement améliorer l’efficacité. Côté offre, une gestion dynamique des sources d’alimentation en fonction de la fluctuation des cours et des volumes disponibles permet en général de faire d’importantes économies.
En résumé, il y a quatre domaines stratégiques à privilégier pour réduire la consommation d’énergie :
- Meilleure conception des nouvelles installations ;
- Investissement dans la refonte des procédés pour gagner en efficacité énergétique ;
- Amélioration des stratégies d’exploitation et de maintenance ;
- Gestion efficace des différentes sources d’alimentation pour réduire les coûts ou consommer moins d’énergie.
Les entreprises doivent coordonner leurs actions dans ces quatre directions pour résoudre véritablement la question de leur efficacité énergétique et de leur bilan carbone.
Conception axée sur l’efficacité énergétique
La façon dont est conçue l’ingénierie de procédés répond à toute une série d’objectifs, à commencer par le rendement et la qualité, la flexibilité afin de gérer les fluctuations de matières premières et l’évolution des produits au fil du temps, la sécurité et le respect de la réglementation en matière d’émissions, la stabilité opérationnelle et la minimisation des dépenses. Lorsque l’efficacité énergétique est reléguée au dernier rang des priorités, les conséquences négatives affectent l’usine tout au long de sa durée de vie.
Le temps est l’ennemi numéro un d’une conception privilégiant l’efficacité énergétique. Aujourd’hui la pression sur les délais concerne la plupart des projets, quelle que soit leur taille. Le procédé le plus éprouvé ou le plus facile à concevoir (d’un point de vue fonctionnel) implique une phase de développement. En analysant l’intégration thermique (analyse Pinch) à ce stade précoce, on obtient des avantages importants sur toute la durée de vie de l’installation. Des procédés efficaces sur le plan énergétique permettent non seulement de diminuer les coûts du cycle de vie mais aussi de limiter les dépenses à travers la réduction des contraintes d’évaluation. Ils contribuent également à économiser l’énergie pour les besoins de chauffage et le refroidissement.
Trois méthodes permettent une meilleure optimisation de la consommation d’énergie dès la phase de conception :
- L’utilisation d’un logiciel intuitif d’analyse (Pinch) et d’optimisation de l’intégration thermique incorporé à la simulation des procédés permet au concepteur de rapidement rechercher, visualiser et sélectionner la conception la plus efficace du point de vue énergétique.
- La modélisation détaillée de l’échangeur de chaleur lors de la simulation des procédés permet au concepteur d’examiner les compromis possibles entre la taille, l’efficacité et l’opérabilité de l’échangeur afin d’arbitrer au mieux entre dépenses d’investissement et coût d’exploitation.
- L’optimisation de l’interaction entre les blocs de chauffage et de refroidissement et les principales unités de traitement telles que les colonnes de séparation, en utilisant les méthodes d’optimisation intégrées aux simulateurs de procédés leaders du marché.
La maîtrise de l’énergie est capitale, non seulement pour les vastes procédés de masse de la pétrochimie et de la production d’engrais mais aussi pour les nouveaux procédés de bioconversion en quête de viabilité commerciale. 30 % des économies d’énergie sont réalisées dès la phase de conception des procédés en alliant les connaissances et les outils logiciels appropriés.
Refonte des installations existantes
Il existe diverses opportunités d’amélioration de la consommation énergétique des installations existantes et bon nombre des solutions possibles entraînent d’ailleurs un meilleur rendement. Les mêmes outils que ceux utilisés au stade de la conception initiale sont à la disposition de l’ingénieur qui cherche à économiser l’énergie et à améliorer le fonctionnement des installations. Les principales occasions sont notamment lors de la reconfiguration ou du remplacement d’un échangeur de chaleur ou de l’installation d’un échangeur supplémentaire, lors des interventions de maintenance préventive plus poussées visant à réduire l’encrassement des échangeurs et lors de la modification des paramètres de fonctionnement et de la configuration du matériel pour gagner en efficacité.
Un bilan énergétique complet d’une installation peut faire apparaître des dizaines d’opportunités d’amélioration, dont certaines impliquent des dépenses d’investissement importantes et d’autres des compromis au niveau de la production pour à la fois consommer moins d’énergie et obtenir un meilleur rendement.
Stratégies de fonctionnement et de maintenance
Il existe toute une gamme de pratiques et de stratégies de fonctionnement pour améliorer collectivement la consommation d’énergie d’une usine :
- Affichage des indicateurs de performance clés de la consommation énergétique
Les tableaux de bord visuels des performances d’une usine constituent le point de départ de toute amélioration du fonctionnement. Lorsque tous les opérateurs, les agents de maintenance, les responsables de la planification et les managers connaissent l’impact de leur action sur la consommation et la facture énergétique de leur usine, chacun prend conscience de sa responsabilité individuelle dans la maîtrise de l’énergie.
- Maintenance des échangeurs de chaleur
L’encrassement des échangeurs de chaleur entraîne une hausse de la consommation d’énergie et une baisse du rendement. Des modèles adaptés de procédés et d’échangeurs peuvent être combinés aux données de l’usine en temps réel afin de prédire l’encrassement et mettre en place un calendrier de maintenance qui réduit le nombre de pannes et améliore la consommation d’énergie et le rendement. Plusieurs entreprises ont documenté l’impact positif de ces mesures sur leur chiffre d’affaires.
- Planification efficace de la production et de la consommation d’énergie
Lier la planification de la production et celle de la consommation d’énergie permet de garantir l’alimentation des installations et de limiter les besoins de torchage de l’excédent de gaz combustible et de ventilation de l’excédent de vapeur. Cela facilite également la prévision des éventuels goulets d’étranglement. Mieux planifier au quotidien et réagir rapidement aux changements tout en améliorant l’exécution des tâches sont des conditions essentielles. La gestion de l’offre lors du processus de planification de la production, le coût de l’énergie et les objectifs d’émission deviennent partie intégrante de la planification. Des avantages peuvent être obtenus sur le plan opérationnel en planifiant la consommation d’énergie en entrée et en sortie (c’est-à-dire les besoins en énergie des équipements et des installations, la planification des matières premières, l’achat d’énergie à l’extérieur ou l’utilisation des sources disponibles en interne). Les outils de gestion prévisionnelle les plus en pointe peuvent faciliter l’évaluation des compromis à faire entre production, sources d’énergie, coûts et émissions afin d’optimiser véritablement les opérations.
- Optimisation en temps réel et contrôle avancé
Un système de contrôle avancé peut gérer un procédé afin de réduire les écarts par rapport à son déroulement normal et contribuer ainsi à faire fonctionner l’usine au plus près des performances voulues. Cela permet de réduire la facture énergétique globale pour ce procédé et de mieux gérer les émissions dans les limites autorisées. L’optimisation en temps réel peut être associée à des systèmes de contrôle avancé pour réduire encore plus la consommation d’énergie. L’application d’un modèle de processus analytique en continu aux données de production permet d’adapter en permanence la stratégie opérationnelle en fonction des performances réelles de l’usine.
Faire la différence
Le niveau de priorité accordé par les entreprises à la gestion de l’énergie varie en fonction de l’évolution et de l’incertitude des cours. C’est une attitude à courte vue. A long terme, les investissements dans la réduction de la consommation d’énergie seront rentabilisés sur toute la durée de vie d’un équipement. En obtenant les mêmes résultats en consommant moins d’énergie, les entreprises peuvent mettre en place des processus plus efficaces et adopter les technologies de pointe pour gagner en performance. La maîtrise de la facture énergétique a pour corollaire l’avantage d’améliorer le rendement des procédés. Elle a également des effets positifs en termes de développement durable. Parce qu’elles consomment beaucoup d’énergie, les usines de traitement seront de plus en plus sous l’œil du législateur et du grand public en ce qui concerne leur empreinte carbone.
Pour bon nombre d’entreprises, l’impact positif des économies d’énergie sur leur rentabilité ne fait en général aucun doute. La difficulté est d’identifier clairement les opportunités d’amélioration et leurs implications en termes de dépenses et de fonctionnement. Les logiciels avancés de simulation, d’analyse, de planification, d’organisation, d’optimisation et de contrôle des procédés optimisent la consommation d’énergie en gérant les opérations à l’échelle de l’entreprise. Une réduction des dépenses peut être obtenue en mettant en place des mesures opérationnelles plus efficaces sur le plan énergétique, ce qui se traduit par une hausse de la production et une baisse des émissions.
En adoptant les meilleures pratiques, les entreprises améliorent la façon dont elles se procurent, achètent et consomment de l’énergie. En exploitant leurs systèmes d’alimentation existants avec un minimum de dépenses et un maximum de fiabilité, elles optimisent leur plan de production tout en tenant compte des contraintes environnementales, organisationnelles et techniques qui évoluent sans cesse. Les responsables peuvent s’appuyer sur ces bonnes pratiques pour prendre des décisions calculées, mesurées et pérennes, tout en respectant la réglementation et en améliorant les normes de production. En prenant en compte tous les systèmes énergétiques, les logiciels de gestion d’énergie leaders du marché fournissent aux entreprises de procédés la solution idéale pour dompter l’ogre énergétique depuis la conception jusqu’à la production et améliorer considérablement leur marge.