Christophe Sirugue, secrétaire d’Etat chargé de l’industrie, souhaite renforcer le programme de modernisation du tissu productif français porté par l’Alliance Industrie du futur. Il se fixe trois priorités.
Christophe Sirugue, secrétaire d’Etat chargé de l’industrie, remettait hier, à la Cité des sciences et de l’industrie à Paris, les trophées des « Vitrines de l’industrie du futur ». Cette labellisation par l’Alliance Industrie du futur distingue les projets industriels les plus exemplaires dans la modernisation et de la transformation numérique de leur modèle. Ils étaient douze à la recevoir aujourd’hui (lire encadré tout en bas).
« L’Industrie du futur est l’enjeu central de la reconquête industrielle. Elle doit tirer parti des nouvelles solutions technologiques de la Nouvelle France Industrielle pour inscrire l’ambition de modernisation au cœur des filières industrielles. Elle est l’antidote au fatalisme et offre à toutes les entreprises les moyens d’un renouveau », déclarait le Ministre. Ce fut surtout pour lui l’occasion d’annoncer le renforcement du programme de modernisation du tissu productif français, porté par l’Alliance Industrie du futur, à travers trois priorités, dont la première est d’ancrer cette dynamique sur le terrain en se concentrant sur les PMI et les ETI.
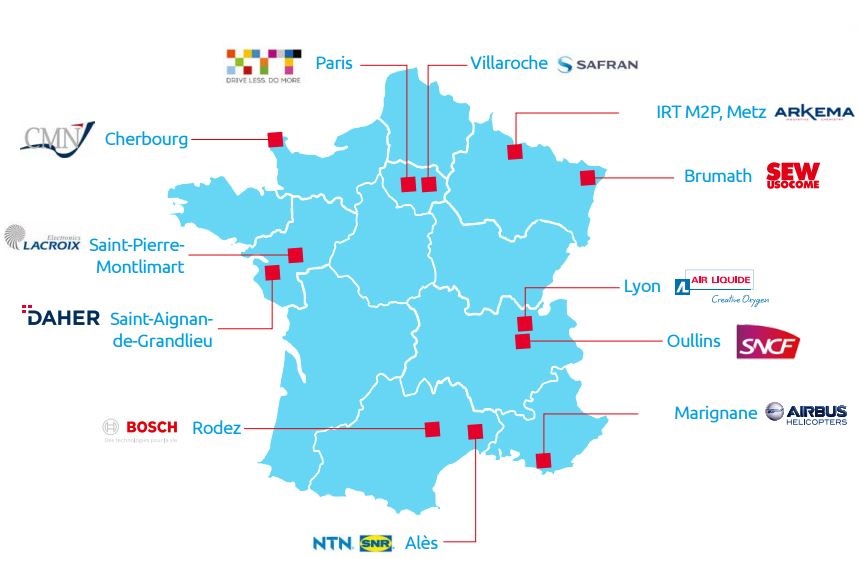
12 vitrines labellisées industries du futur © Alliance du Futur et ministère
Plus de 4000 bénéficiaires d’ici à fin 2017
L’ambition du programme d’accompagnement de ces entreprises sera ainsi portée de 2 000 à 3 400 bénéficiaires d’ici à fin 2016 (puis à 4 300 à fin 2017). Le Ministre a souhaité que l’ensemble des filières industrielles du Conseil national de l’industrie (CNI) soient associées. Cette nouvelle ambition sera inscrite dans les schémas régionaux de développement économique, d’innovation et d’internationalisation des Régions. Treize « ambassadeurs » (un par région) ont été nommés par l’Alliance Industrie du futur : ils iront à la rencontre des chefs d’entreprise dans les régions pour les sensibiliser aux enjeux de l’industrie du futur. C’est d’ailleurs, à Saclay, le 28 septembre, lors de l’inauguration du Factory Lab du CEA qu’il avait fait en avant-première cette annonce.
Les Régions poursuivent ainsi le pilotage du déploiement de ce Plan sur leurs territoires notamment dans le cadre des futurs Schémas régionaux de développement économique, d’innovation et d’internationalisation des entreprises (SRDEII) et intensifieront leurs travaux communs avec l’Alliance pour l’industrie du Futur.
Un grand salon « national » pour l’industrie
La deuxième priorité est de faire connaître et valoir les solutions technologiques françaises en France et à l’étranger (d’où les trophées). Le Ministre a ainsi dévoilé le programme du salon international « Industrie du futur » qui aura lieu du 6 au 9 décembre 2016 à Villepinte, autour de démonstrateurs, de conférences et d’expositions. A terme, les trois salons dédiés à l’industrie (Industrie du futur, Smart Industries et Midest) devraient d’ailleurs être réunis sous la marque « Confluence Industrie du Futur ».
Enfin, la troisième priorité –et pas des moindres- sera de préparer les évolutions des métiers et des compétences en adaptant la formation initiale et continue. Le Ministre a demandé au CNI et à l’Alliance Industrie du futur de lui faire des propositions d’ici la fin de l’année.
« Un tel vent positif n’a jamais autant suscité l’adhésion et la mobilisation de tous. Je crois que notre force, notre énergie et notre intelligence collective sont les leviers de notre reconquête industrielle », a conclu Philippe Darmayan, le président de l’Alliance Industrie du futur ». On ne peut que le souhaiter à l’heure où certaines usines (STX Saint-Nazaire, Airbus Helicopters Marignane qui fait partie des 12 « vitrines », Alstom Belfort…) font largement parler d’elles. Car, comme le rappelait récemment Patrick Artus, l’économiste en chef de Natixis, dans une note (1) sur la désindustrialisation de notre pays : « La France affiche à peu près le même niveau de gamme de production que l’Espagne, mais avec des coûts de production 20 % supérieurs ! »…
(1) France : L’impossible réindustrialisation. Flash Economie, 21 septembre
Les 12 vitrines de l’industrie du futur© Airliquide.com Air Liquide : des technologies numériques de rupture pour optimiser la production Bosch : l’utilisation de biomasse locale pour limiter les gaz à effet de serre SNCF : Le digital au service de la maintenance industrielle Daher : Une ligne haute cadence de pièces thermoplastiques Constructions mécaniques de Normandie (CMN) : le chantier naval du futur SEW-Usocome : Les processus de production de demain XYT : une start-up de construction automobile au modèle d’affaires innovant Arkema : chef de file pour une future filière de composites thermoplastiques recyclables (atelier de production : IRT M2P) NTN SNR : projet « Usine idéale », disposant de lignes de production réinventées autour de l’opérateur, à Alès (30). Lacroix Electronics : une production et une « supply chain » digitalisées, pour la compétitivité de la French Tech dans l’IOT, à Saint-Pierre-Montlimart (49) Airbus Hélicoptères : projet « Digital Shopfloor » pour un déploiement d’outils numériques performants et harmonisés dans les ateliers de production de Marignane (13). Safran : une ligne d’assemblage innovante pour assurer la compétitivité du moteur LEAP, à Villaroche (77) (sources : Alliance du Futur et ministère) |
Lire également notre dossier complet sur l’Usine du futur.